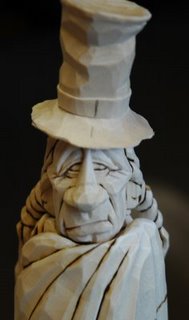
Now that we have the Body of the figure almost completed we can begin on the head and hat. Notice I said the body was "almost" completed. We still have to match it to the head! Remember that it's cold out there so we want his head pulled down into the blanket. To do that will take some extra fitting.
There are a ton of photos associated with this post as I wanted to really go over a number of steps which, I think, really make a good character. Even though we're carving a caricature, facial structure is just as important as when carving a realistic figure. There has to be bone struction to support the features and I'll explain and show this as we move through this lesson.
One important thing about this carving....As he is cold and sad we want the weight of the snow and his other worries to really bear down on him. To show this all lines on the face will curve downward, i.e., the eyebrows, the eyes, the mouth. Even the brim of the hat and the direction of the hat's tip amplify this mood.
As indicated on the original drawing the braids and hat are done seperately as are the feather and the two little ear rings. The braids will be epoxied in place and then carved. The feather and ear pendants will be carved and then glued in place once the figure is painted.
So, we've got lots of ground to cover so we'd better get started!!